‘Fleet’ is the representation of a population of repairable products that are currently in use out in the field by customers. Repairable is the keyword differentiating a ‘fleet’ from commonly known consumer product ‘units’.
Items like laptops, phones, tires, and glass panels that are manufactured and sold to customers are ‘Units’. Whereas items such as Fuel Cells Systems, Cars, and Compressors are called ‘Fleet’. The differentiation is key in understanding the type of reliability program needed. Thus, we can summarize the conditions for an item to be ‘repairable’ as
- Maintenance work (replace or repair or overhaul) can be done feasibly & effectively to restore its function
- OEM provides after-sale support to customers throughout the usage time
A business keeping up the above two promises to a customer faces the daunting task of managing the Reliability of the fleet. If the fleet assets fail often, it is not only expensive to repair but also lowers user satisfaction leading to shrinking market size & profits.
For an organization designing, manufacturing & maintaining fleet products, how to effectively manage the Reliability of the fleet? By combining the Design for Reliability (DfR) and Reliability-centered Maintenance (RCM) principles. This fused framework deserves a separate article to expand but the junction step of ‘Monitor & Control’ is where the significance of the method lies. It provides the required balance between allocating more budget to the Product Design team or the Fleet Maintenance team in efforts to improve reliability.
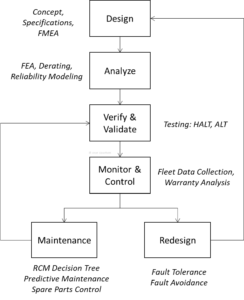
The Severity and Consequence of a failure mode from the Risk Analysis (ex: FMEA or similar) decide if the improvement action is maintenance work or a redesign of the component. For redesign: Fault Tolerance (redundancy) and Fault Avoidance (high strength) are the two avenues used in increasing the robustness of the design. For maintenance: RCM Decision tree helps in deciding the type of maintenance task between Scheduled Maintenance or On-Condition Maintenance or Run-to-failure.
When the fleet is monitored in real-time using sensors onboard then the decision path is altered to favor Predictive Maintenance, where maintenance is performed only when the fleet’s condition warrants it prolonging the usage life. The resulting reduction in maintenance cost multiplies over hundreds of fleet products to have significant savings. Analyzing all the sensor readings from hundreds of fleet products is an ‘analysis problem’ overcome by deploying appropriate Machine Learning algorithms (ML/AI).